IV.
The Dawn of Tungsten.
In the Robertson lamp the carbon filament made its nearest approach to perfection. The longest life and the most light for the least electricity; these were the ideals aimed at. All that could be done with carbon, was done; and if today the Robertson lamp is becoming a thing of the past it is only because science is always advancing.
Even at the birth of the carbon lamp, inventors had a prophetic eye on something better. Lamps had been made with a filament of fine platinum wire, but platinum had the drawback of melting when it was hot enough to give off a brilliant light, otherwise it would have been better than carbon. The promise of platinum -which was a metal easily drawn into very fine wires of great strength-made inventors think of other metals.
So, in the patent specifications of those early days, we find scheduled all sorts of substances, possible and impossible. Had patent law permitted, these pioneers would doubtless have made a general claim to all things on the earth and in the sea and under the earth. Anyway it is very interesting to note that carbon was always looked upon as faute de mieux, and that the parents of the carbon lamp had a vision of the brighter day when a lamp with a metal filament would take its place. The day came eventually, though the dawn was a very slow one.
Most inventors kept the eye of expectancy on certain rare metals, which seemed to have just the properties requisite for a more efficient electric lamp, but working along quite different lines, Professor Nernst invented a lamp with a tiny pencil of "rare earths" which glowed brilliantly under the action of electricity. The Nernst lamp had, however, certain practical disadvantages, and its brief promise did not divert other inventors from the pursuit of a suitable metal filament. It was Auer Von Welsbach who produced the true prototype of the modern metal filament lamp. This had a filament of osmiurn, and in its attractive potentialities, as in those of the Nernst and other lamps, The General Electric Company, Limited, took the keenest interest, but certain practical drawbacks prevented it from becoming a commercial success.
Tantalum was the first metal which really reached the commercial stage. It was destined, however, to have a very brief career, as although the tantalum lamp was a great improvement on the carbon lamp, it had certain limitations. Over it, like a shadow, lay the promise that tungsten would make a still more efficient lamp.
For a time, nothing could have seemed more hopeless than the attempt to make a practical filament out of tungsten. Tungsten ore is found in association with tin, both in Cornwall and in Australia; and when, after a process of refining, pure tungsten is obtained, it is in the form of fine powder. Making "ropes of sand" seemed to be just as easy as transforming this powder into the thin tough filament required for an electric lamp. Nevertheless, remembering how cotton-wool was changed into hard carbon, inventors set to work on the apparently impossible.
Their first attempt was heroic, and in a large measure successful. They mixed the powder with a binding material into a paste and the paste they squeezed through a diamond die-that is to say, through a minute hole in a fragment of diamond. A fine thread was thus formed, and the binding material was afterwards burned out by means of an electric current. The result was a fragile filament with one redeeming virtue-it gave four times the light of a carbon filament for the same amount of electrical energy.
Fragile, it certainly was, and so much so that many people looked upon it as commercially hopeless. Filament breakages on the way from the factory to the user were in the early days simply appalling. In fact, the game seemed hardly worth the candle. Nevertheless, there was one man who believed wholeheartedly in the future of tungsten lamps, and who proved his faith by putting a million of them on the market. He was Mr. Hugo Hirst.
In this act of faith, which roused the whole electrical world to the importance of the new development, the Osram lamp was born. Its birth necessitated the building and equipping of a new factory, the designing and construction of new machines, the training of hundreds of new operators and the solution of a host of new problems of chemistry, metallurgy, production and sale. A complete new industry grew up alongside the Robertson factory and threatened it with ultimate eclipse.
V.
From Squirted Filament to Drawn Wire.
It is at once the fate and the fascination of invention that no sooner is, one triumph achieved than a greater rises to take its place. The fir st form of Osram lamp, with its "squirted filament" of tungsten, was indeed a triumph against tremendous odds, and it had reached a high degree of robustness when the miracle of making tungsten wire was performed.
This miracle has become a daily commonplace in the Osram Lamp Works, but it will never lose its freshness and its wonder to those who remember how utterly impossible it once appeared to be. In our description of these works we shall tell, step by step, how it is done. For the moment we shall merely note that the material used in all modern electric lamps is drawn tungsten wire, which is among the toughest materials known. The anxiety which once haunted the makers of tungsten lamps has vanished for ever. Tungsten lamps have proved capable of withstanding the incessant vibration of a railway train and the shocks of gunfire on a battleship.
Even with this achievement, however, the spirit of invention did not rest content. It has already been noted that a tungsten lamp is about four times as efficient as a carbon lamp; that is to say, it gives about four times as much light for the same consumption of energy. It does so by virtue of the fact that the tungsten filament "burns" much better than the carbon filament. The whole story of improvement in electric lamps is summed up in the words "higher temperatures."
Anyone can prove this by using a lamp intended for a certain electrical pressure on a circuit where the pressure is much higher. The lamp will burn with an amazing brilliance, but it will burn out all the quicker.
It was found, however, that if an inert gas, such as nitrogen, were introduced into the bulb, the life of such an over-brilliant lamp would be prolonged. Out of this discovery came what is known as the "Gasfilled" electric lamp. Actually the gas used is mainly argon, the existence of which in the atmosphere was discovered by the genius of the late Lord Rayleigh.
The gasfilled lamp is the most economical lamp yet produced. In the larger sizes-which were the first to be made-it is twice as economical as the ordinary vacuum type of lamp. It is in fact so economical that it has put the electric arc lamp-once the light for large spaces-on the scrap heap except for special purposes.
To sum up, the progress which began with the Robertson lamp of 1893 has culminated in a source of light which is about six times as efficient.
VI.
The Osram Organisation.
Facetious accounts have
been given of the wonderful machines in certain American
pork factories, where pigs enter at one end and bacon,
sausages, hair brushes and other finished porcine products
emerge at the other end. But it may be said quite seriously
that the Osram electric lamp factory is a place where
glass bulbs and tungsten ore enter, to emerge later
in one of the manifold forms of completed electric
lamps.
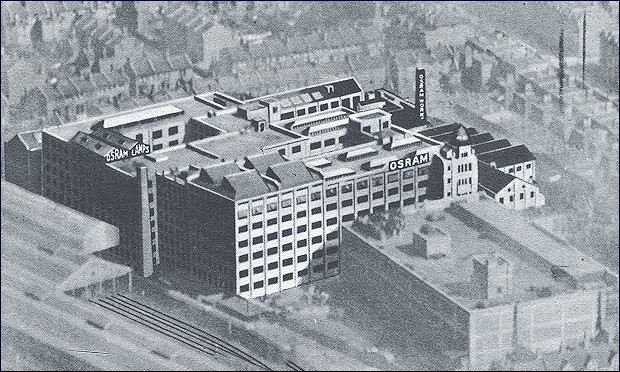
THE OSRAM-G.E.C. LAMP WORKS, BROOK GREEN, HAMMERSMITH. LONDON, W.
(REPRODUCED FROM AN AERIAL PHOTOGRAPH)
The Osram Lamp Works
may thus be looked upon as a huge lamp-making machine.
It is a very complex machine, because it must turn
out every kind of lamp, for every purpose, and every
electrical pressure. Nevertheless it is an orderly
machine, although its system may not be clear to visitors
who pass rapidly through one vast room after another
and see in each an almost bewildering series of operations.
In designing the huge blocks of buildings that
lie to the left of the main entrance and form the main Osram factory, the object
in view was in each block to keep each floor-or section, as it is called-as far
as possible to one type of lamp. We may picture each section as a stream along
which electric lamps move from beginning to completion. All these streams are
fed from a common fountain-head; or rather, two fountainheads-one of glass and
the other of metal.
The first lies in the basement, which we find
loaded with packages containing lamp bulbs, glass tubing and rod. The bulbs are
made at the Lemington Glass Works (near Newcastle-upon-Tyne) acquired many years
ago by The General Electric Company, Limited, in pursuance of its determination
to manufacture everything required for electric lamps, whilst the tubing and
rod come from the recently built glass works at Wembley, Middlesex.
The crates from the glass works are unloaded from
wagons on to an electrically-driven conveyor which carries them to the basement,
where they are opened and the material examined and cleaned. Cleanliness, by
the way, is a vastly important thing in lamp making; even a finger mark on a
lamp stem may destroy the perfection of the lamp.
The material is taken up lifts at one end of each
block, to the various sections. This upward movement of glass meets a downward
movement of metal from the other fountain-head - the tungsten wire department
on the uppermost floors. Metal and glass are thus supplied to each section at
one end and travel along in the same direction towards completion at the other
end, where collecting lifts take the finished product to the despatch department.
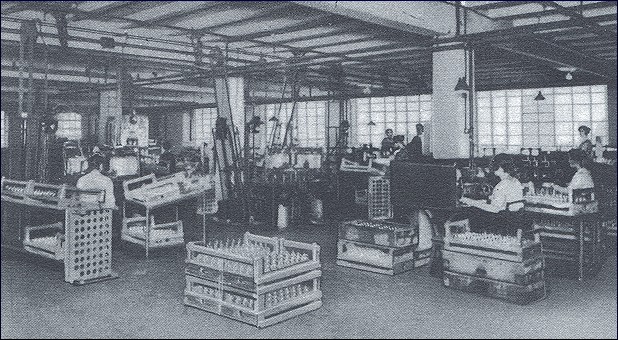
A FACTORY WITHIN A FACTORY-ONE
OF THE THE "SECTIONS"
IN THE HAMMERSMITH WORKS.
VII.
The Production of Glass.
For over a hundred
years glass has been made at Lemington, and the Lemington
factory therefore enjoys the full benefit of the
hereditary craftsmanship so characteristic of British
Industries. The blowing of bulbs is an operation
requiring a high degree of skill, which comes only
by expert training and long practice. A small quantity
of molten glass is taken on the end of a blow pipe,
the operator rolls it to and fro on an iron-plate,
blows in a little air in stages to make a small blob
of glass expand into a pear-shaped hollow mass, and
finally blows the glass to the lamp bulb shape in
a mould.
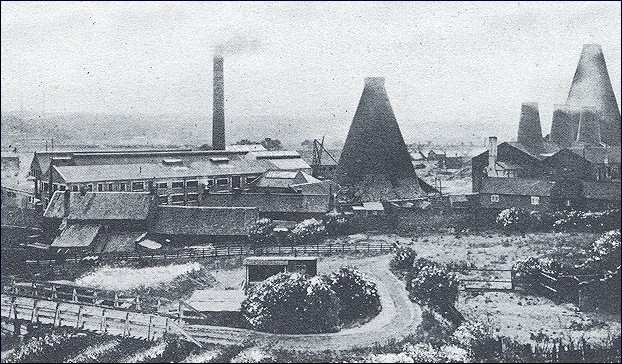
LEMINGTON GLASS WORKS OF THE G.E.C. WHERE OSRAM BULBS ARE MADE.
Millions of lamp bulbs have been made
by this process year after year at Lemington. During
the war, in fact, the Lemington Glass Works supplied
practically the whole of the lamp bulbs required in
Great Britain, thus rendering a national service of
the highest order. Since then, with the increase in
the demand for Osram lamps, Osram enterprise has gone
a step further, and has taken advantage of the latest
developments in mechanical science by installing at
Lemington two of the wonderful Westlake Automatic Bulb-blowing
Machines. "Wonderful" is not too strong an adjective
to apply to these machines which even trained and experienced
engineers watch with fascination, and describe with
enthusiasm. Iron arms flash into a glass-pot, pick
up the right quantity of molten glass by suction and
transfer it to blowpipes, which reverse and swing and
revolve in uncanny imitation of the craftsman's action.
Compressed air is supplied at the right moment; the
vivid pear-shaped molten bubbles are automatically
closed in moulds ; and in another instant the moulds
fall apart in their cooling baths, leaving the bulbs
suspended. A series of clips revolving on an endless
chain receives the bulbs, and carries them on through
an adjacent annealing furnace, the rough necks left
by the machine being cracked off by an ingenious device
specially designed for this purpose.
The Westlake Machine, an invention which took
five years to bring to perfection, is a remarkable asset commercially. Driven
by an electric motor, it is controlled by one man, does efficiently all the processes
- of the skilled worker, and saves an immense amount of labour.
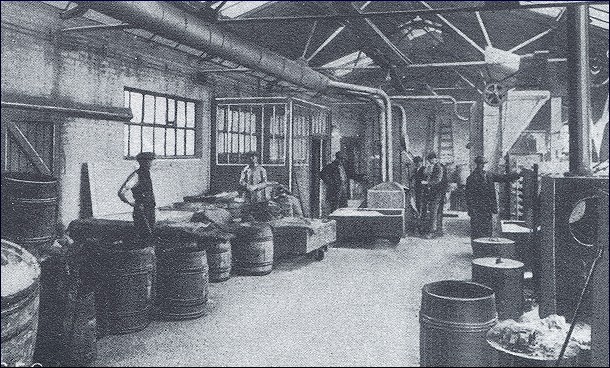
MIXING ROOM AT THE LEMINGTON GLASS WORKS.
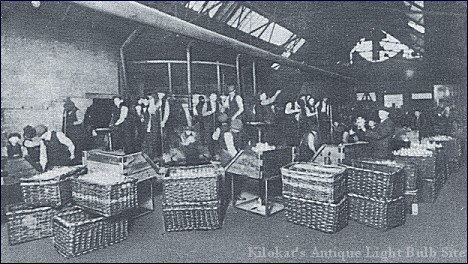
BLOWING OSRAM BULBS BY HAND.
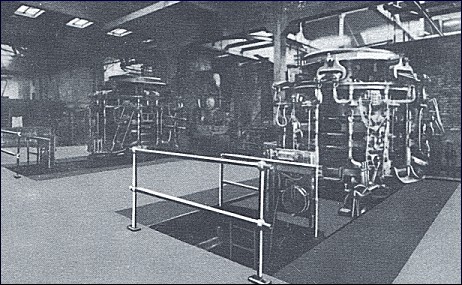
BLOWING OSRAM BULBS BY AUTOMATIC MACHINERY.
A similar policy of complete manufacturing
independence also led to the construction, shortly
after the war, of an additional works at Wembley, for
the production of glass tubing, where the whole of
the Osram Lamp Works requirements in this direction
are now met. At present the equipment of these works
is producing only glass tubing, but provision has been
made for adding, when the appropriate time comes, the
manufacture, on a large scale, of lamp bulbs as well.
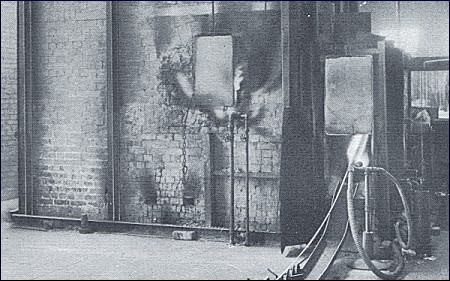
TUBE FURNACE AT THE OSRAM-G.E.C. GLASS WORKS, WEMBLEY, SHOWING
GLASS TUBING BEING DRAWN OFF MANDRIL.
VIII.
The Tungsten Laboratory.
In order to follow
the growth of an electric lamp in its due order,
we must travel from the basement straight to the
roof, where, in, a well-lit, and airy laboratory,
the modern alchemist transmits useless-looking stone
into valuable tungsten.
Every part of the process is carried out in the
laboratory under the most expert supervision, since the utmost care is needed
to ensure that the product will be absolutely right for lamp making.
The ore is crushed and ground to a powder, which is washed with acid to remove
impurities and to convert the calcium tungstate contained in the ore to tungstic
oxide. Treatment of this oxide with ammonia produces a colourless solution of
ammonium tungstat from which a bright yellow powder is precipitated by a further
addition of hydrochloric acid. This powder, which consists of pure tungstic oxide,
after "cooking" in a series of pans, becomes a dry material, not unlike yellowish
Plaster of Paris.
One stage more is needed to change this material
into the metal itself. A quantity is placed in a long tube of quartz traversed
by a stream of hydrogen and heated by gas flames, by which treatment the oxide
of tungsten is reduced to metallic tungsten. From this fiery furnace there is
taken a fine grey-black powder, notable for its great weight. This is pure tungsten-the
sand from which ropes have to be made, the dust which we are to see later drawn
into tough wires of an almost invisible fineness.
Simple as this process of metal-making appears
to the visitor, it has its scientific secrets. On one of these we may half-open
the door of revelation. Although the filament of a modern electric lamp is described
as a tungsten filament, it is not wholly tungsten. The Osram Lamp Works found
that the admixture of the tiniest proportion of certain substances would make
the tungsten filament much more durable.
Curiously enough, tungsten itself plays a similar
part in the making of special steels. The admixture of a little tungsten in steel
makes that steel tremendously tough. Just as steel is mixed with tungsten, so
tungsten in the lamp factory is mixed with certain other substances.
Incidentally this department also produces, in
an almost identical manner, the molybdenum metal which, as will later be described,
is used for making the filament supports.
continue...
|